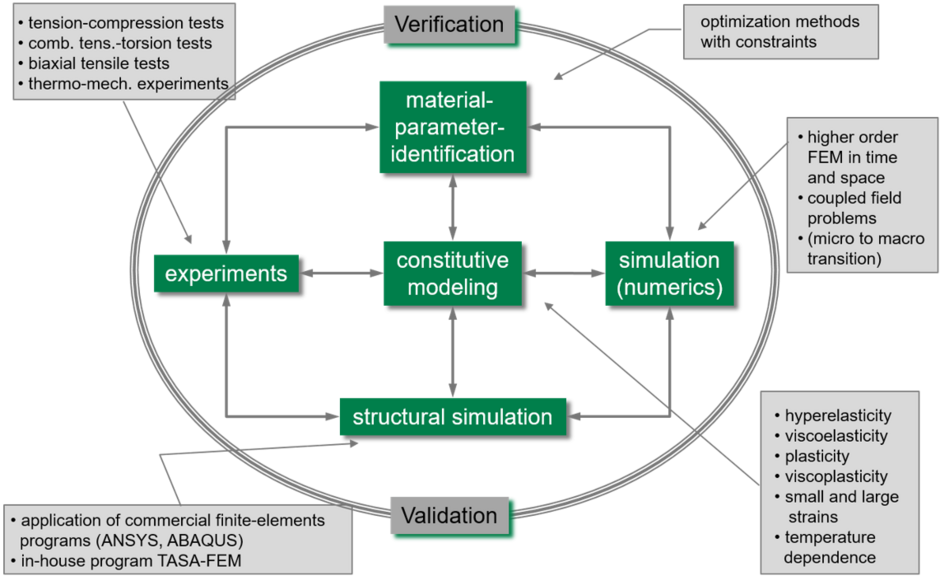
What do you initially imagine by the term "mechanics"? Moving cogwheels, connected crank drives consisting of rods and rotating drives? The mechanics of today have only a marginal connection with these more construction-oriented ideas. Mechanics today is much more multifaceted, demanding and interdisciplinary. In addition to the engineering subfields of fracture mechanics, vibration engineering and machine dynamics, structural mechanics, environmental mechanics and fluid mechanics, solid mechanics, which should be seen here as equivalent to continuum mechanics, is one of the major specialist disciplines. Within the field of solid mechanics, we distinguish between experimental mechanics, material theory, i.e. the modeling of material properties using mathematical models, and computational mechanics. Material theory is extremely broad in scope. The rather traditional modeling of the three-dimensional mechanical deformation behavior of a solid under external process-dependent loads, which includes not only metals, plastics and elastomers, but also soils, concretes or types of wood, is nowadays coupled with thermal, electrical, magnetic and chemical influences and extended with microphysical considerations. In addition, the biomechanics of animal and human tissue is one of the expanding fields of research. The solid mechanics professorship in Clausthal deals with the physical modeling of small and arbitrarily large distortions of different materials, such as those used in forming technology, the tire and rubber industry and in plastics technology. These models are developed on the basis of combined tensile, compression and torsion tests under thermal loads, see Fig. 1.
Two further aspects are immediately apparent: The developed models contain material parameters that have to be adapted to the performed experiments, which is coupled with the issue of optimization procedures. The second problem is associated with the integration of the material models into commercial or in-house code finite element programs in order to be able to calculate components realistically.
Fig. 2. shows the five main pillars of the professorship. These are integrated into the current research branch consisting of verification and validation. Verification is understood as the development of numerical and analytical methods for checking the implementation in finite element programs and the solutions generated with them and implies the development of highly accurate and efficient calculation methods. In validation, the numerical and physical models are compared with component tests, whereby the quality of the prediction must be specified in advance. Within this concept formation, the working group has developed work (reference to literature here) on material parameter identification, the development of experiments and material models and the new development of adaptive time integration methods within the finite element method.
The in-house solid mechanics laboratory, the PC pool shown in Fig. 3 and the staff support the implementation of these objectives.